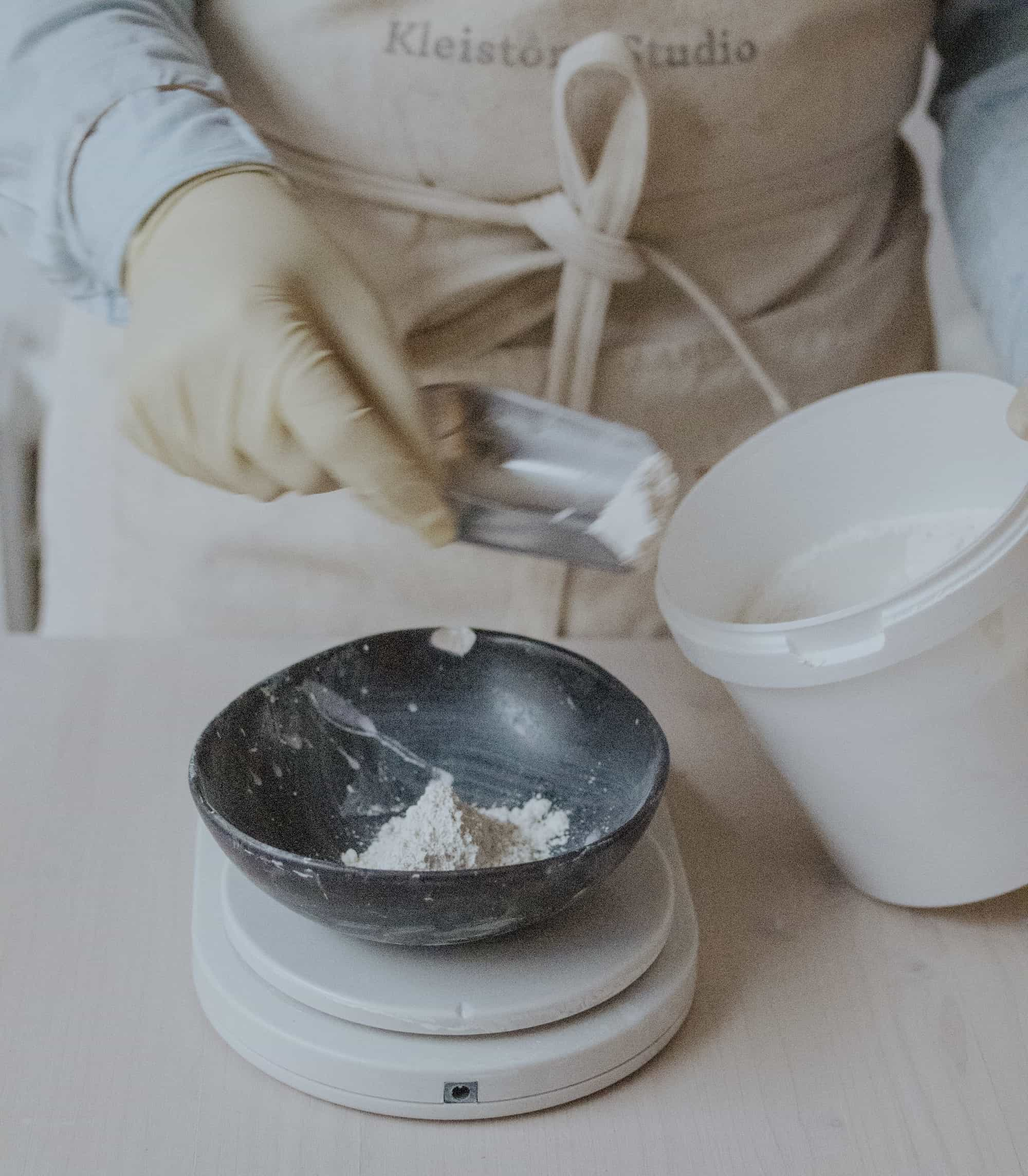
Demystifying glazes, their contents and the firing process
We are often asked by students about the contents of glazes. The assumption is always that glazes contain “toxic chemicals” and that they work in somewhat mysterious ways. Our approach to teaching and sharing knowledge with the community is aimed at removing this aura of mystery around materials, and glaze is the material that appears to be the most shrouded in myth.
- Glaze is made of chemicals in the same way the air we breathe is made of chemicals. Pretty much everything around us is chemistry. Glazes, like clays, are made of minerals, rocks. The materials we use to make our clays and glazes are extracted from the earth and combined in specific compositions to achieve a specific result. All glazes need pretty much the same type of ingredients: glass formers (to create the glass that is the glaze) and fluxes (to reduce the melting temperature). It doesn't matter what glaze you are making: you will need those ingredients in some amount.
- Glazes do not work in mysterious ways. The process of melting the materials that make up the glaze takes place at high temperatures (in the kiln), but it is very much not a mystery. Your pieces go through a chemical transformation when they are fired and all of this can be explained, understood and controlled by understanding what goes into a glaze and how the various components affect the result.
- We can control our results by controlling various aspects of the process:
- The way a piece is made and bisqued: is your piece very thin? Was it thrown, hand-built or slip cast? Bisque temperature affects the way glaze is applied, the application process itself and the final result.
- The composition of our glazes: if you know what’s in your glaze, you can learn to make tweaks to control the result and trouble shoot issues. We teach a basic glaze chemistry class where you can learn to understand and evaluate glaze recipes.
- The application of your glaze: application makes a huge difference in the outcome and we find that it is without fail the most common problem area. You can be using the same glaze and seeing different results due to a variable in how the glaze has been applied. Was it dipped for the same amount of time? Is the water content stable for each application? Was the glaze stirred and left to rest? We teach a glazing masterclass that covers basics of glaze application and glaze theory.
- The firing process itself: probably the thing we like to blame the most and that has the least responsibility in the whole process. Electric kilns are meant to keep heat inside so your pieces reach temperature and all those minerals can melt and form the glass. Some areas of the kiln may be hotter than others, which may very well account for some small differences in results, but usually and apart from some special firing schedules, kilns pretty much do their thing and work with what we give them.